DIY Speakers
10-liter bass reflex cabinet for the AIYIMA 4"
single driver
August 3, 2023
The Bluetooth speaker used in my desktop died recently and I saw
an opportunity to build a pair of desktop speakers and use the
idling SMSL Q5 PRO digital amplifier to play music again.
Recycled pallets
I've been using recycled pallets for a few CNC projects when my
Snapmaker A250 was new. These are 18mm thick and about 140mm wide
which is just right for a small cabinet of 10-liters in volume. I
used WinISD to create the simulation and determine the port size and
length which is pretty straightforward.
Using Fusion 360, I created a model of the speaker box, and since
the intended use is for near-field desktop, I placed the port in
front.
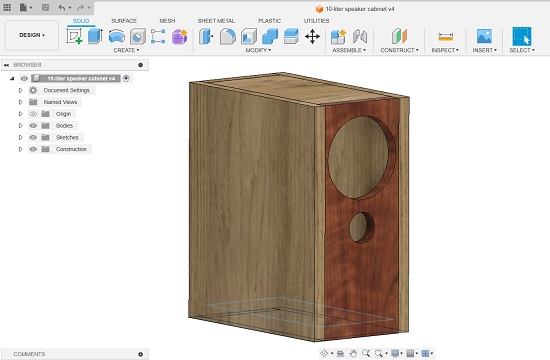
Lack of tools, again
I have another project for the Mark Audio Pluvia 7 drivers, and
during the creation of the cut list, I found out I have enough stock
left over for this small 10-liter box. So instead of my trying to
cut the pallets straight using my jigsaw, I sent the order to my
supplier.
Here are the cuts:
- 4 pieces 130mm x 336mm (front/back)
- 4 pieces 130mm x 260mm (top/bottom)
- 4 pieces 336mm x 296mm (sides)
In the end, these 18mm thick American Mahogany plyboards will become
the cabinet to these AIYIMA drivers.
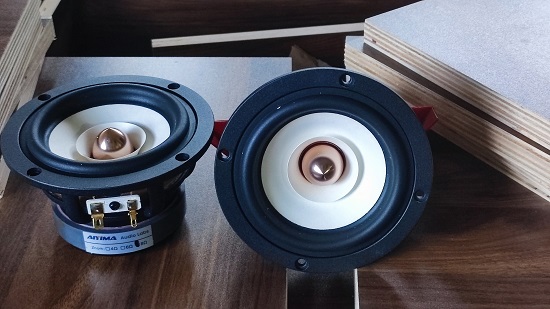
The front panel is milled with the Snapmaker A250 and this time, no
mishaps occured.
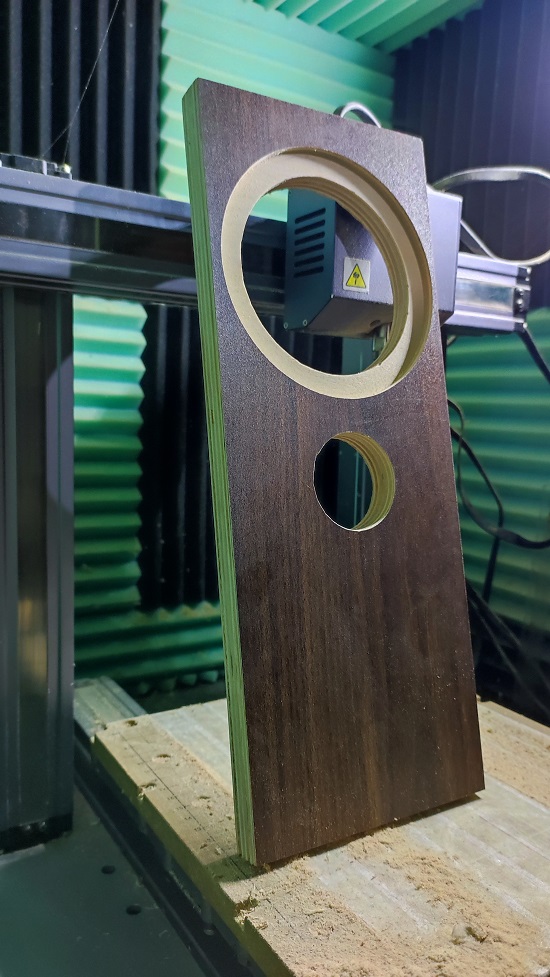
Bond... Titebond
So yes, I glued them all together using Titebond, and of course
clamps. This time no clamps failed!
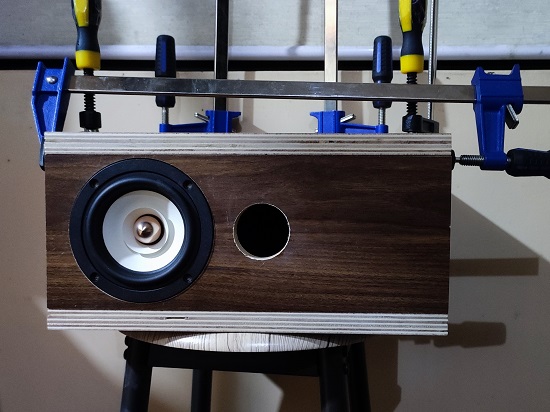
I like how it turned out, sanding will be the next step.
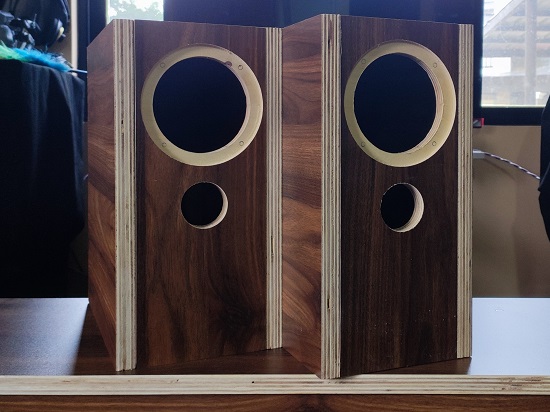
The port tube is 45mm in diameter and 134mm in length, as calculated
by WinISD. The Cetus Mk3 3D printer is suitable for this job. I
wanted the burgundy color but I'm short on filament so only the
first 60 layers in burgundy and the rest in boring silver color.
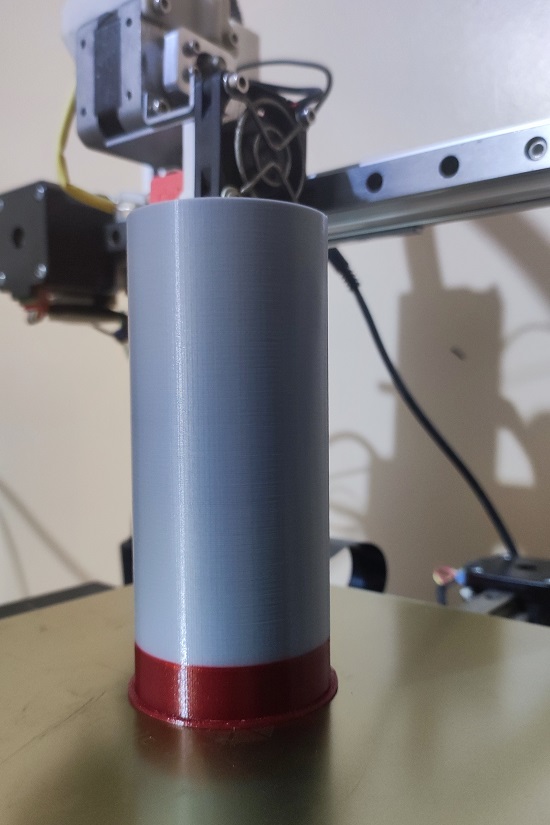
Test fit of tubes and drivers for hole marking and drilling.
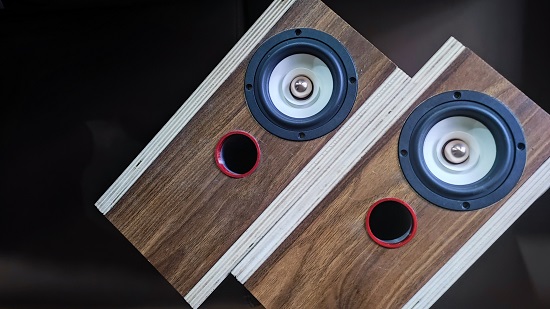
It's now time to install the binding posts and secure the internal
wiring. These binding posts are screw type so it was easy securing
the IXOS 6006 Gamma Geometry speaker wires that are left over from a previous project.
Finally, taping the FIBERFILL on all sides except the front.
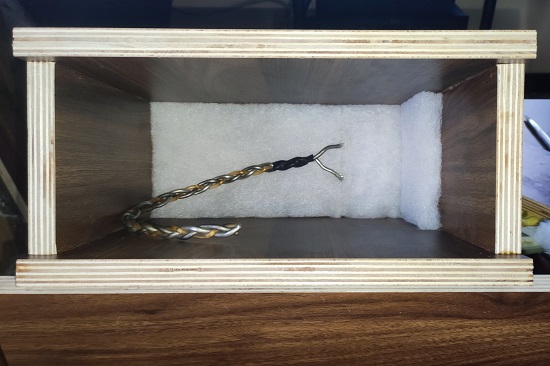
After 48 hours, I started cutting and test fitting the acoustic
foam. Based on the specifications, the acoustic foam is applied only
to the top and rear panels but I also intend to line up the side
panels with the polyester fiber.
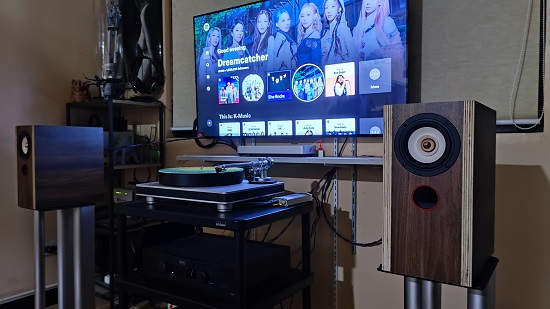
Sound check
TBD
Materials used
Here's the list of materials to complete this project.
Tools used